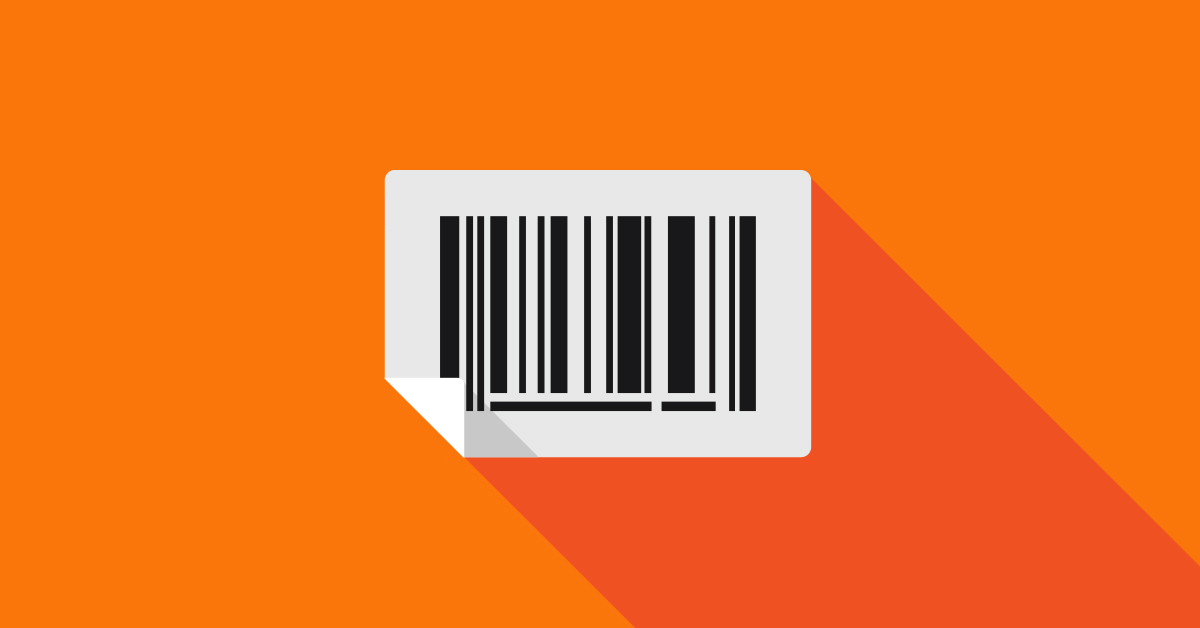
For people new to operating a retail store and managing inventory, it can be difficult to understand how barcodes, UPCs and SKUs work and what purpose they serve.
That’s what we’re going to clear up for you in this post. Learn what they are, the differences between them, what purpose they serve and their benefits.
In this post, we’ll cover:
- What is a barcode?
- How do barcodes work?
- Types of barcodes
- The benefits of using barcodes
- What is a UPC?
- What is the purpose of a UPC
- What are the advantages of UPCs
- UPCs vs. SKUs
Generate barcodes, fast
Tired of manually managing your inventory? Create unlimited unique barcodes for your inventory today with our free barcode generator tool. It's easy to use and compatible with all scanners.
What is a barcode?
A barcode is an image that consists of a series of parallel black and white bars that can be read by a barcode scanner. Barcodes are applied to products to quickly identify them. Among their many uses, barcodes are typically used in retail stores as a part of the purchasing process, in warehouses to track and manage inventory and on invoices to help with accounting.
What is a barcode scanner?
A barcode scanner (also referred to as a barcode reader) is a device that captures and decodes the information contained by a barcode. Traditional barcode scanners consist of the following four components:
- Light source: This helps the barcode read and accurately decode the information contained in a barcode.
- Lens: This scans the barcode.
- Photoconductor:This translates optical impulses into electrical ones.
- Decoder:This analyses the barcode’s data and sends it to the scanner’s output port.
After capturing the information, barcode scanners link to a host computer or tablet and transmit that information in real-time, without additional human intervention. This helps retailers automate data collection processes and reduce human errors like inventory tracking and processing point of sale transactions.
How do barcodes work?
In a nutshell, a barcode is a way to encode information into a visual pattern (those black lines and white spaces) that a machine (a barcode scanner) can read.
The combination of black and white bars (also referred to as elements) represents varying text characters that follow a pre-established algorithm for that barcode (more on the types of barcodes later). A barcode scanner will read this pattern of black and white bars and translate them into a line of test that your retail point of sale system can understand.
Types of barcodes
There are two types of barcodes: 1-dimensional (1D) and 2-dimensional (2D).
1-dimensional (1D) barcodes
1D barcodes are a series of black and white bars that can store information like a product’s type, size and color. You can find 1D barcodes on the top of universal product codes (UPCs) of a product’s packaging. This helps track packages through package delivery service providers like UPS and FedEx, the US Postal Service and Canada Post.
2-dimensional (2D) barcodes
2D barcodes are more complex than 1D barcodes. They can include more information than just text, like price, inventory levels and even a product image. There are plenty of barcode scanners that support 2D barcodes. While not all barcode scanners can read 2D barcodes, Lightspeed Retail POS is compatible with several wireless barcode scanners that support 2D barcodes.
The benefits of using barcodes
While barcodes were originally developed to speed up the sales and transaction process, they come with several other benefits.
Improved accuracy
Using a barcode to process a product’s data is much more accurate than having a sales associate manually enter that data, which is prone to human error.
Real-time data
Because of the speed at which the information is processed, data about inventory levels or sales is available immediately.
Reduced training requirements
Thanks to a barcode scanner’s ease of use (just point and click), employees don’t need much training on how to use one.
Better inventory management
With improved accuracy and real-time data, retailers benefit from faster cycle counts and more accurate inventory turnover estimations.
Low cost of implementation
Generating barcodes is quick and simple, plus, the potential savings thanks to improved transaction speed, as well as the improved accuracy of inventory and sales data, retailers can anticipate savings post-implementation.
What is a universal product code (UPC)?
A universal product code (UPC) is a code that’s printed on a retail product’s packaging to help it be identified. There are two parts that make up a UPC: the machine-readable barcode (which is a series of black bars) and the unique 12-digit number located beneath the barcode.
Parts of a UPC
To get a UPC to use on products, a company needs to apply through GS1 AU (the Global Standards Organisation), which manages and assigns UPCs in Australia and globally.
After paying the application fee, GS1 assigns a six-digit manufacturer identification number; that becomes the first six digits of the UPC for all of the company’s products and identifies the item’s manufacturer.
The subsequent five digits of the UPC are the item number, which identifies the product itself. Each company should have a person responsible for issuing item numbers, ensuring that the same number isn’t used more than once and that numbers associated with discontinued products are no longer used.
Most consumer products have several variations based on their size, colour, etc. Each variation needs its own item number. For example, a box of medium-sized t-shirts will have a different item number than a box of the same t-shirt in size small.
The last digit of a 12-digit UPC is the check digit. It’s found by adding and multiplying several of the UPC code’s numbers to confirm to the barcode scanner that the UPC is a valid one. If the check digit code isn’t correct, the result is that the UPC code won’t scan properly.
What’s the purpose of a UPC?
UPCs make it easy to identify a product by its name, item type, size and colour when it’s scanned at the checkout. They were initially created to make grocery store checkouts faster, but nowadays they’re also commonly used to help track inventory in retail stores and warehouses.
The advantages of a UPC
There are several advantages, both for businesses and consumers, for using UPCs. Since UPCs help barcode scanners identify a product and its cost, UPCs help improve checkout speed. They effectively remove the need to manually input a product’s information.
UPCs also improve inventory tracking and management. They help merchants know when they need to stock more of a particular product either on their shelves or in stock more in their warehouse.
If ever there’s an issue with a product, UPCs also help merchants find the customers that purchased that product, contact them and issue a recall.
UPCs vs. SKUs
Let’s talk about the difference between a UPC and a stock keeping unit (SKU). While they share some similarities, they aren’t the same thing.
A UPC is a universal product code; it’s meant to identify a product regardless of where it was sold. For example, if you buy a t-shirt online or through a local retailer that also sells the same product, that t-shirt will have the same UPC.
A SKU, however, is an internal product inventory code that’s unique from one company to the other. If you were to compare the SKU of the same product at two different stores, you’d see that they were different.
If you’re confused as to whether you’re looking at a UPC or SKU, the UPC symbol is the barcode label or bar coding on the back of a product, whereas the SKU is typically found on a store’s unique shelf pricing.
If you were to try looking up a product online, using the product’s UPC will help you find it across numerous retailers, whereas the SKU would only find the product under the business using that specific SKU.
UPCs can be valuable for suppliers and manufacturers to track the inventory they sell to different retail merchants, whereas SKUs are valuable for merchants to track and manage their inventory in a way that’s unique to their business.
Both SKUs and UPCs are advantageous for retailers: SKUs for their customisability and UPCs for their universality. Many businesses use a mix of UPCs and SKUs. To learn how to add items to your inventory with UPCs and SKUs in Lightspeed POS, check our retail support page that covers the topic in greater detail.
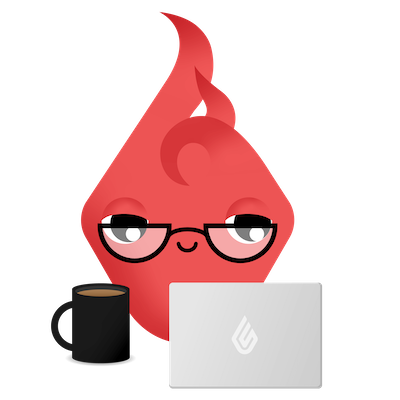
News you care about. Tips you can use.
Everything your business needs to grow, delivered straight to your inbox.